What Causes Bubbles To Form
In the process of plant extraction, the formation of foam is mainly due to the liquid containing active substances that can reduce the surface tension, such as saponins, proteins, polysaccharides and resins. These substances can reduce the surface tension of the liquid, while increasing the viscosity of the liquid, making the foam more stable and less likely to burst.
In addition, high-speed stirring will mix air into the liquid, especially when the viscosity of the extraction liquid is high, the gas is more likely to stay and form foam; In the process of decompression or vacuum concentration, the dissolved gas in the liquid escapes rapidly, which will also lead to a large number of bubbles.
Changes in temperature also affect foam formation; heating or cooling may decrease gas solubility or change the surface tension of the liquid, thereby increasing the amount of foam. The concentration of the extract is another important factor, with high concentrations of dissolved substances significantly increasing the viscosity of the liquid, making it harder for bubbles to escape, resulting in foam that is more stable and difficult to eliminate.
The influence of the chemical environment on the foam can not be ignored, for example, the pH value of the solution will enhance the foaming ability of some active substances, and the difference in surface tension of different solvents will also affect the formation of foam.
Method of defoaming
Physical defoaming is one of the commonly used methods. For example, slowing down the stirring rate mechanically, or optimizing the design of the extraction equipment to reduce local turbulence, thus reducing the mixing of gases. In addition, heating the extract can reduce its surface tension and accelerate the foam rupture; Vacuum defoaming uses a reduced pressure environment to encourage bubbles to escape, thereby reducing foam accumulation.
The chemical defoaming method can quickly destroy the stable structure of the foam. Adding the right amount of food grade or pharmaceutical grade defoamer (such as silicone oils, polyethers or vegetable oils) to the extraction process is a direct and effective way. At the same time, by adjusting the pH value of the extract, the foaming ability of some active substances can also be inhibited, such as making saponins in a neutral or acidic environment with weak foaming ability.
The biological defoaming method is more suitable for the process that has strict requirements on the composition of the extract. The addition of specific enzymes (e.g., proteases, cellulases) can break down foam-causing proteins or polysaccharides, reducing foam formation at the source. In addition, the formation of foam can be reduced through the selection of bacterial strains and metabolic control during microbial fermentation.
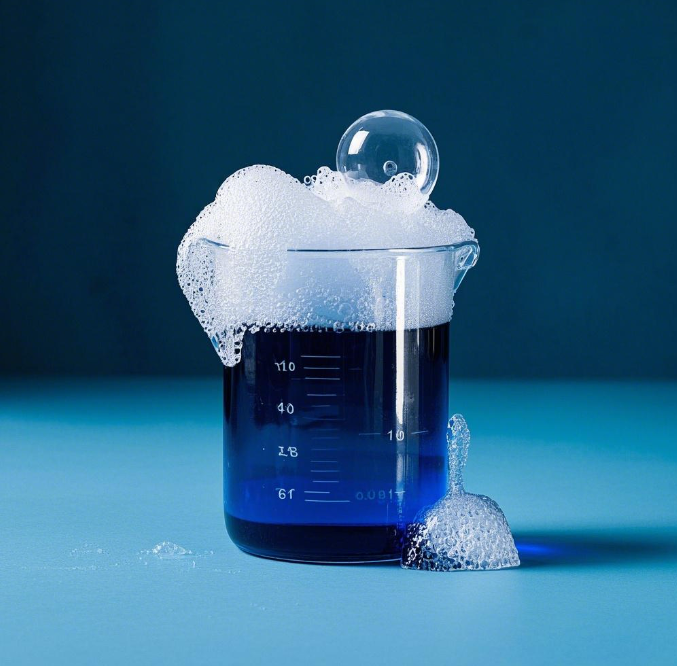
suitable for defoaming in plant extraction process
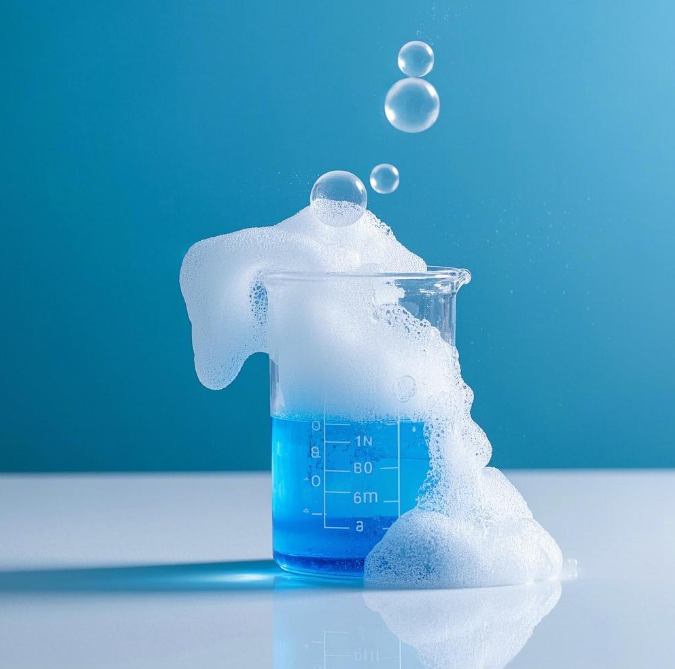
Chemical defoaming: In the production of plant extracts, chemical defoaming reduces the surface tension of the foam by adding silicone, polyether or vegetable oil defoaming agent, which is often used in the extraction, evaporation and concentration stages.
Chemical defoaming has the advantages of high efficiency, simple operation and strong adaptability, but it is necessary to strictly control the dosage to ensure compatibility with the extract, especially in the field of food or medicine, safety and environmental protection defoaming agents should be preferred to ensure product quality and process stability.
Physical defoaming: Physical defoaming is a technique that destroys foam stability by changing process conditions, commonly used methods include heating, cooling and ultrasonic treatment. Heating can reduce the surface tension of the liquid to make the foam burst, cooling can achieve the effect of defoaming by solidifying the foam liquid film, and ultrasonic waves use high-frequency vibration to destroy the foam structure.
This technology is environmentally friendly, adaptable and suitable for a variety of extraction processes, but the equipment investment is high, and it is suitable for scenes with large foam amount or high product purity requirements.
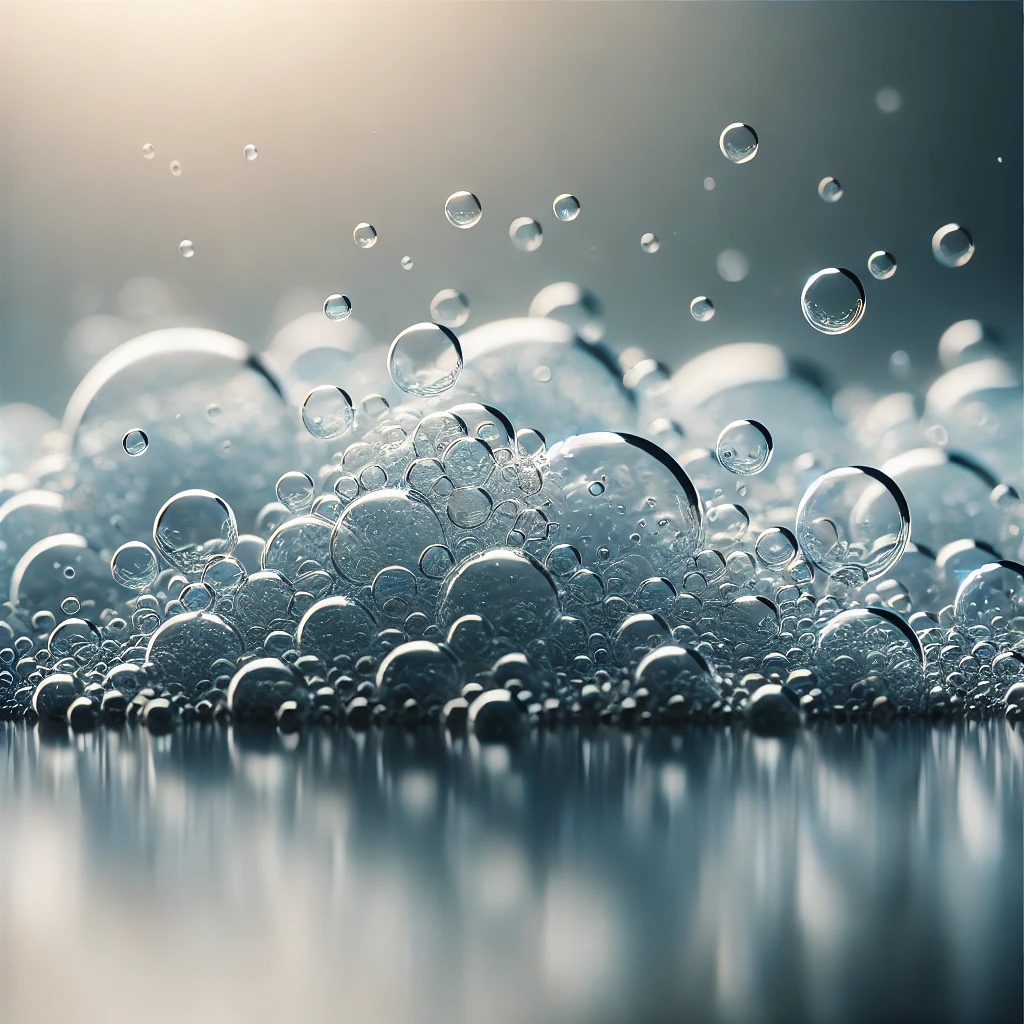
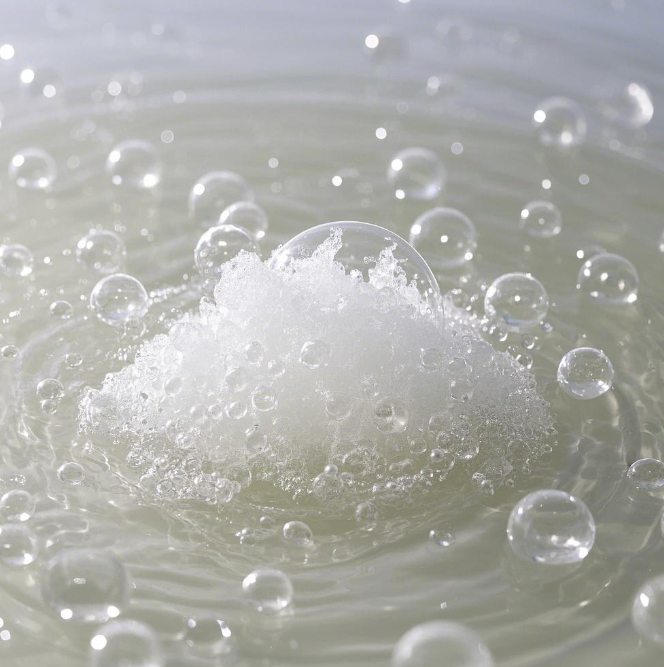
Biological defoaming:Biological defoaming achieves an environmentally friendly and non-toxic defoaming effect by adding biological enzymes (such as proteases or lipases) to break down foaming substances (such as proteins or lipids) in the foam.
This technology is especially suitable for the production of food and pharmaceutical plant extracts with high purity requirements, which can avoid chemical residues and maintain the natural characteristics of the product.However, its application scope is relatively limited, and the cost is high, and it needs to be reasonably selected and optimized according to the actual process conditions.
About Ruiwo:
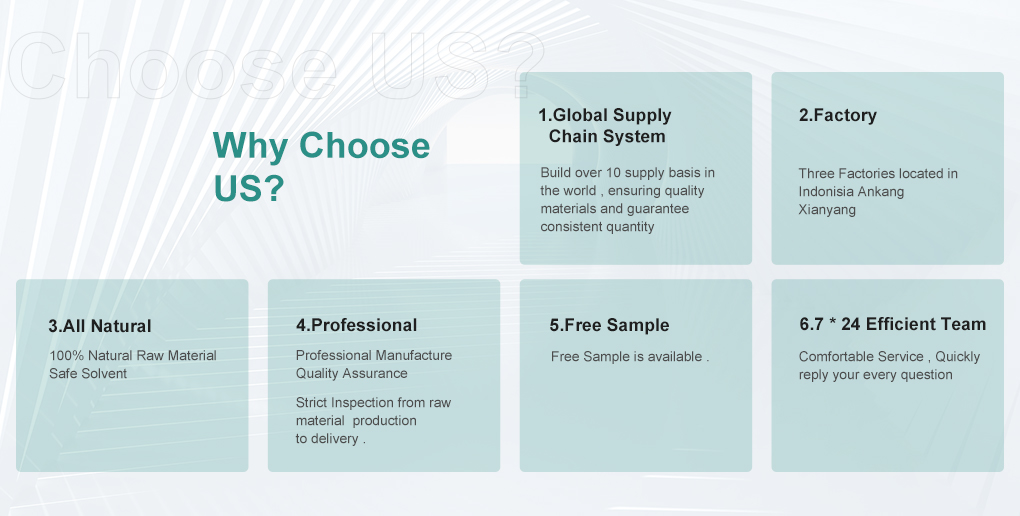
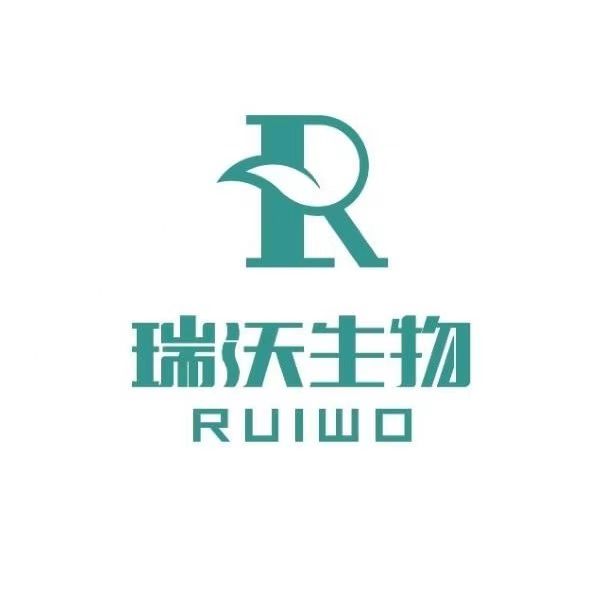
contact us:
Address:Room 703, Ketai Building, No. 808, Cuihua South Road, Xi’an, Shaanxi, China
E-mail: info@ruiwophytochem.com
Phone: 008613484919413 0086-29-89860070
Hours: Monday-Friday: 9am to 6pm
Post time: Dec-31-2024